If you’ve shopped for a welder lately, you’ve no doubt come across the phrase “inverter technology.” But whether you’re new to welding or a veteran of laying down dimes, you might wonder, “Why all the fuss?” Simply put, the introduction of inverter technology has transformed (no pun intended) the world of welding.
Inverter technology in welding, or inverter welders as the machines are often called, is a modern approach to power conversion. Traditionally, welding machines have relied on large, heavy transformers to convert high-voltage, low-amperage AC power from the main power supply into the low-voltage, high-amperage power needed for welding. By contrast, inverter-based welders use electronic circuitry to convert the power with much greater efficiency. These machines convert AC to DC and then invert it back to a desired AC frequency.
Inverter technology is commonly used for Metal Inert Gas (MIG), Tungsten Inert Gas (TIG), and Stick (SMAW) welding processes. It’s preferred by both professional welders and DIY enthusiasts for its versatility, efficiency, and portability. Inverter welders are particularly suited to working conditions where power stability is an issue. Their light weight, portability, and ease of transport make them indispensable for on-site welding jobs and remote locations.
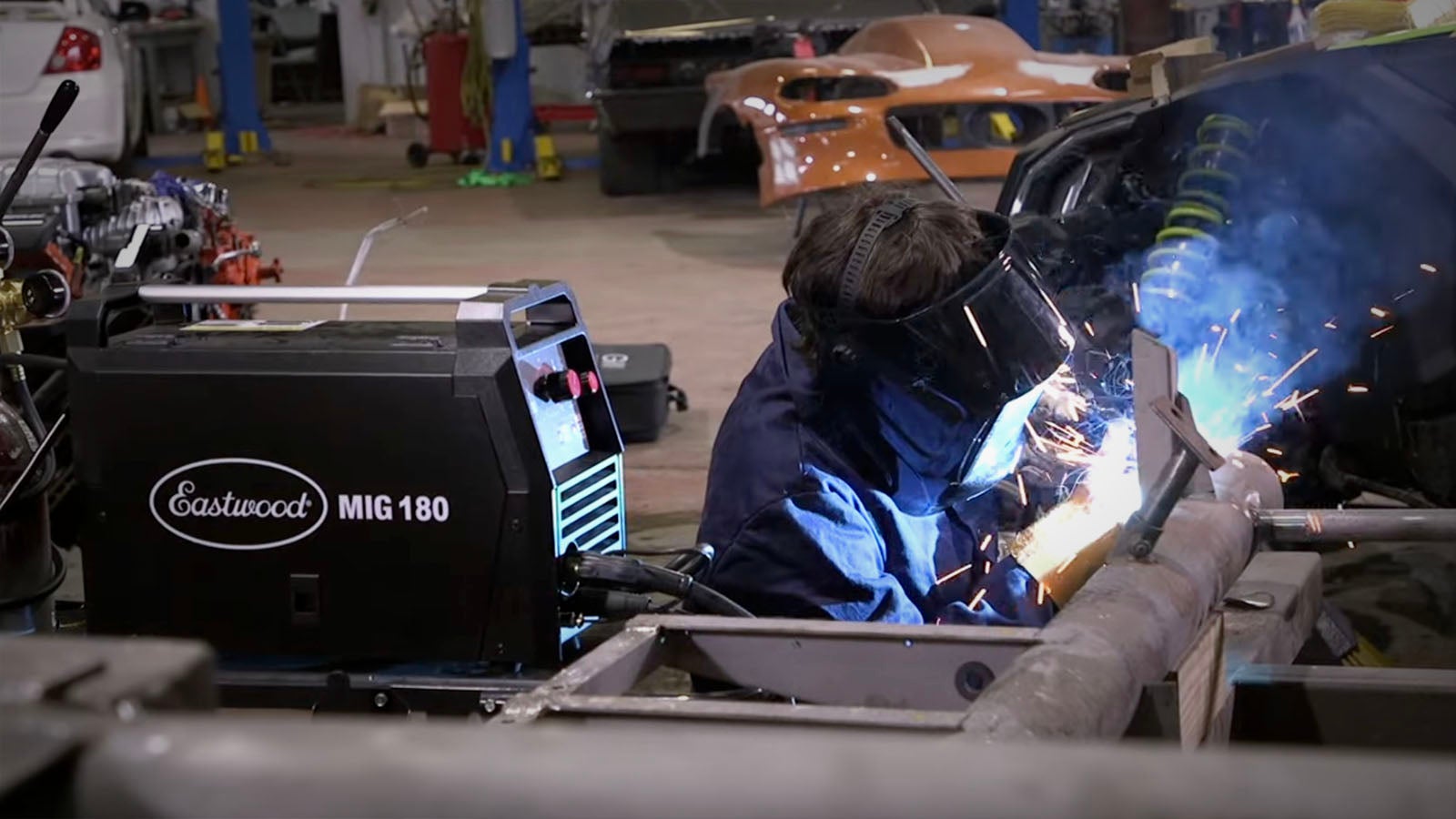
Major Benefits of Inverter Technology
- Portability – Inverter welders are significantly lighter and more compact than traditional transformer-based machines. This makes them easy to transport and ideal for fieldwork or situations where space is limited.
- Efficiency – Inverter welders are more energy-efficient, converting electrical power more effectively and reducing energy consumption. This efficiency also allows them to run on lower power sources, such as standard household outlets, without compromising performance.
- Precise Control – Inverters provide more precise control over welding parameters, such as current and voltage. This leads to higher quality welds, better arc stability, and the ability to weld a wider range of materials with various thicknesses.
- Multi-process Capability – Many inverter-based welders are designed to support multiple welding processes (MIG, TIG, Stick) in one machine, making them versatile tools for different applications.
- Consistent Performance – Inverter welders can maintain consistent output even when operating on fluctuating power supplies, ensuring a stable arc and reducing the likelihood of defects in the weld.
- Improved Arc Start and Stability – The precise control of inverter welders enhances arc starting and stability, making it easier to strike and maintain an arc, especially with challenging materials or in difficult positions.
Inverter technology has rewritten the expectations when it comes to metal arc welding. Compared to old-school transformer-based machines, it offers significant advantages. There’s simply no substitute for their portability, efficiency, control, and versatility.