Whether you’re repairing a vehicle or fabricating something from scratch, you’re likely to work with sheet metal eventually. From fenders and doors to battery trays and truck beds, it makes up most of a vehicle’s non-mechanical components. The problem is thin, flat metal doesn’t offer much in the way of strength by itself. Enhancing stiffness is crucial to achieving a functional, beautiful part.
For manufactured products like body panels, huge presses stamp out perfect pieces in complex, precise forming dies. But how do you make DIY repairs or one-off pieces from scratch with flat sheets? Here we explore six methods to add structure to sheet metal, helping ensure your project posseses both strength and functionality.
Bending
Bending is just what it sounds like – creasing a sheet of metal to achieve a curved or angular shape. This process is commonly used in forming various components such as brackets, flanges, or panels in automotive fabrication. If you’ve ever made a paper airplane, you’re already familiar with how this works.
Brakes or press brakes are the tools commonly used for precision bending. Simple bends can also be achieved using a variety of manual tools, such as hand brakes.
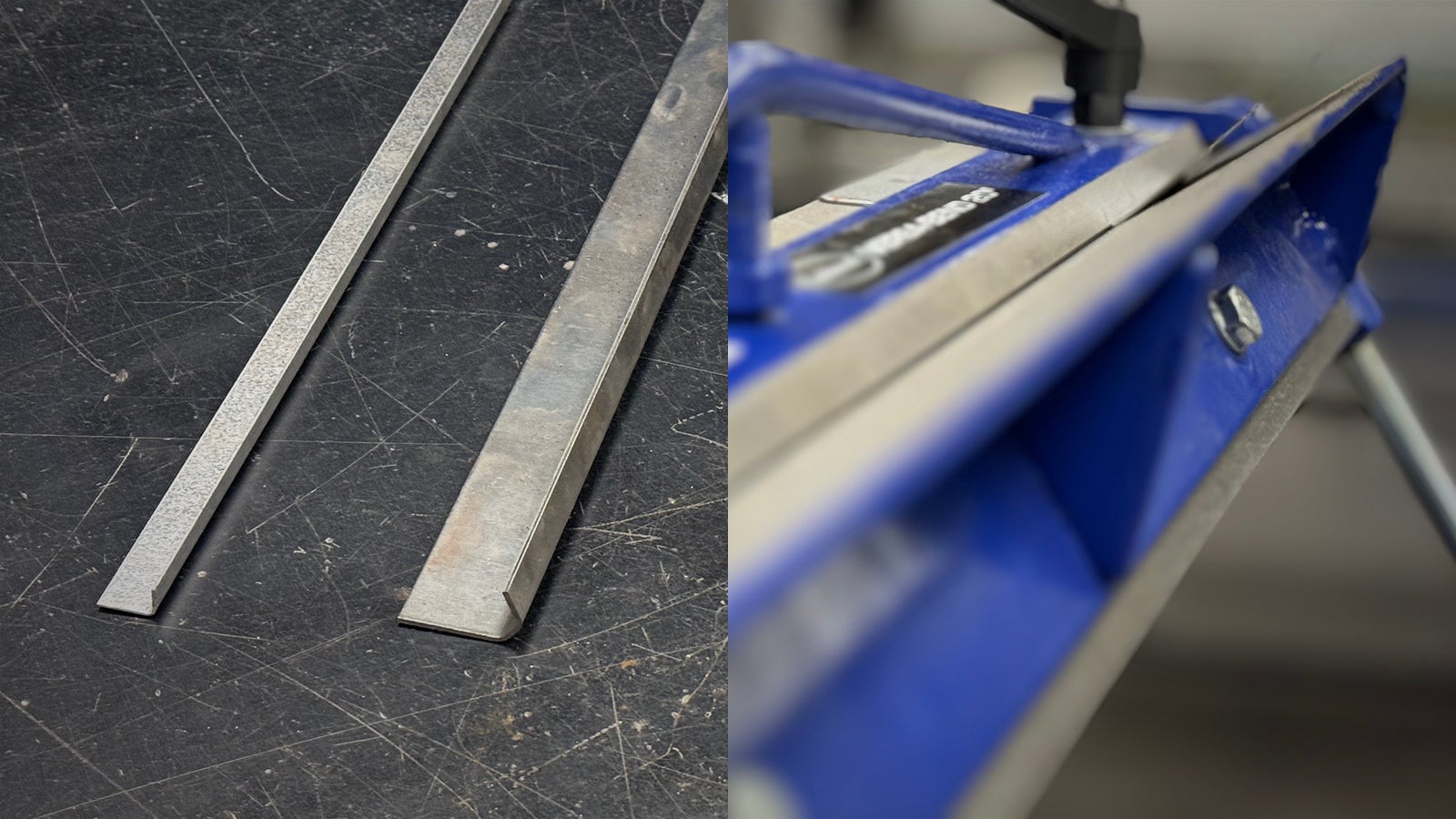
Panel Beating
Panel beating is perhaps the most traditional method of shaping and contouring sheet metal for bodywork, using hammers and dollies to create surface tension. Skilled artisans, commonly known as panelbeaters, carefully strike the metal with special hammers to shape the metal.
Various types of hammers, dollies, anvils, and sand- or shot-filled “beater” bags are used in this process. This can be used to contour roof lines and fenders or create bulges and flares.
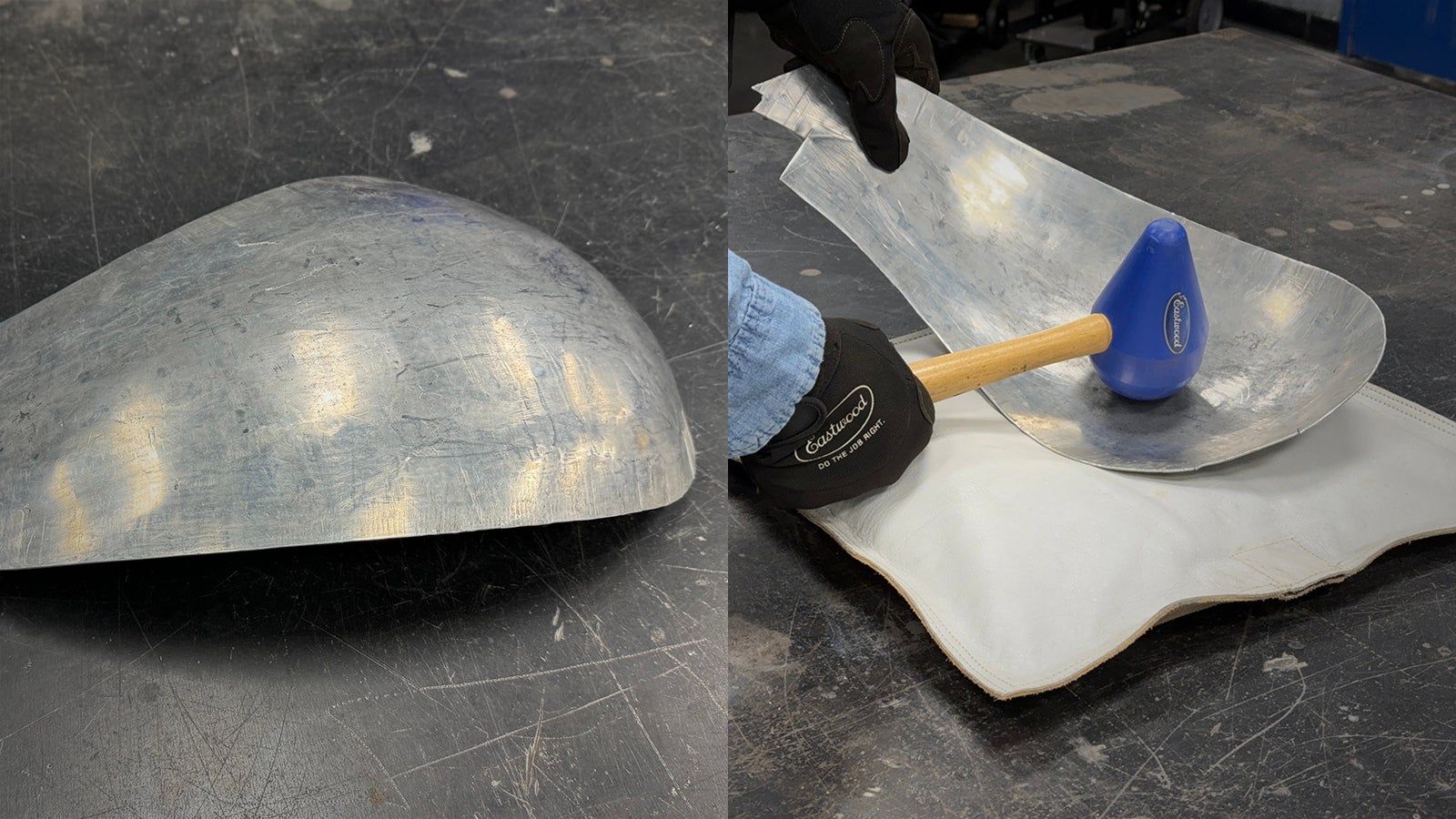
Bead Rolling
Bead rolling adds strength and design features to sheet metal by creating raised or indented lines, known as beads, along the surface. This technique is often employed for stiffening panels or adding decorative elements to automotive parts.
Bead rollers consist of a set of rollers that can be adjusted to create different patterns and sizes of beads. The sheet metal passes between the rollers, and the pressure shapes the desired bead profile.
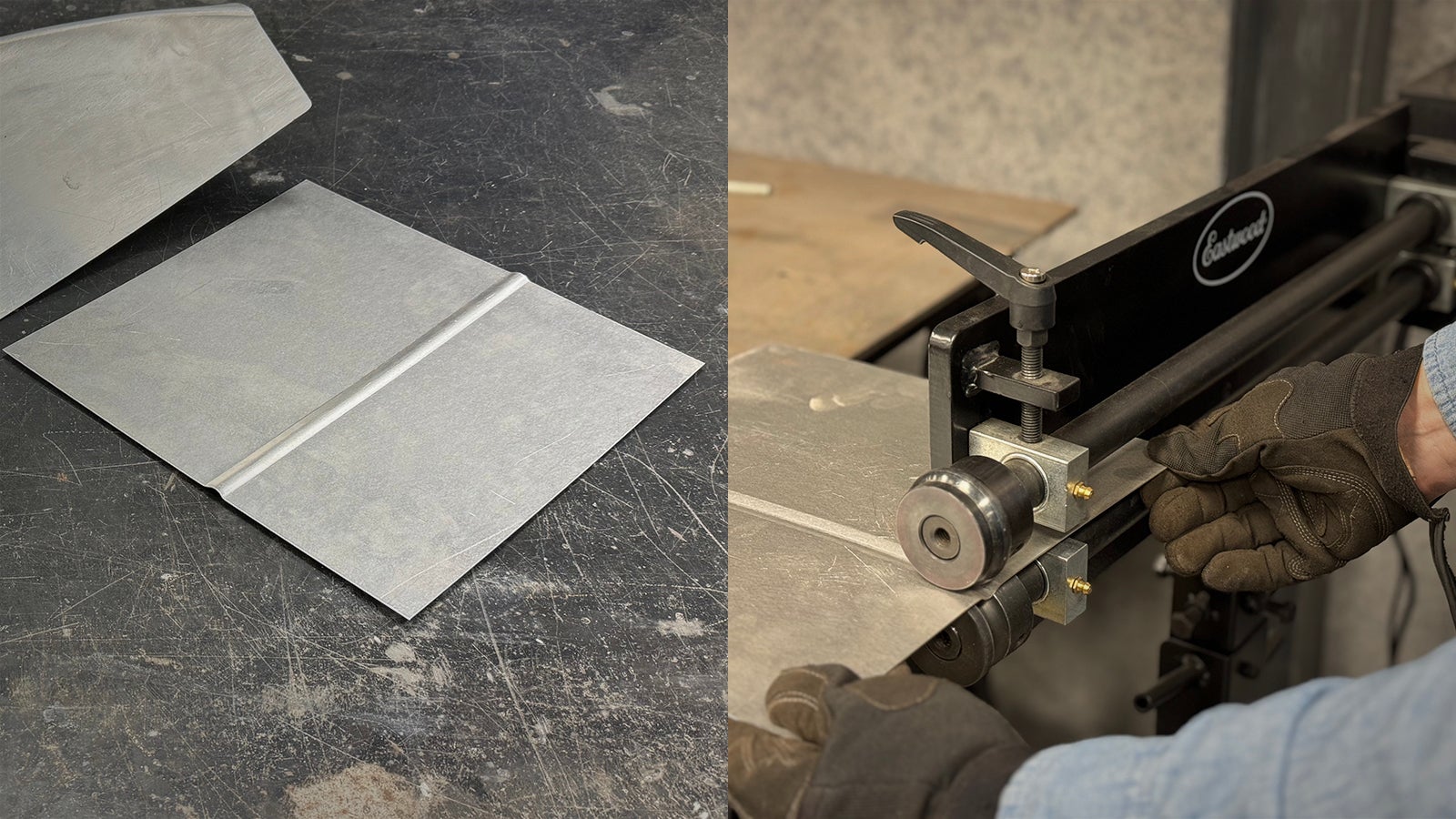
Shrinking and Stretching
These two techniques used to change the surface area of sheet metal without significantly altering its thickness. Shrinking involves gathering metal to reduce the surface by pinching it slightly, like on the edge of a pie crust. Stretching involves expanding it, like when you spread a pie crust into the corners of a pan.
Shrinker and stretcher tools are used for these operations. A shrinker contracts metal while a stretcher expands it, allowing fabricators to control and manipulate the sheet to achieve specific shapes. This technique is also used to smooth the edges of metal that has puckered from other shaping work.
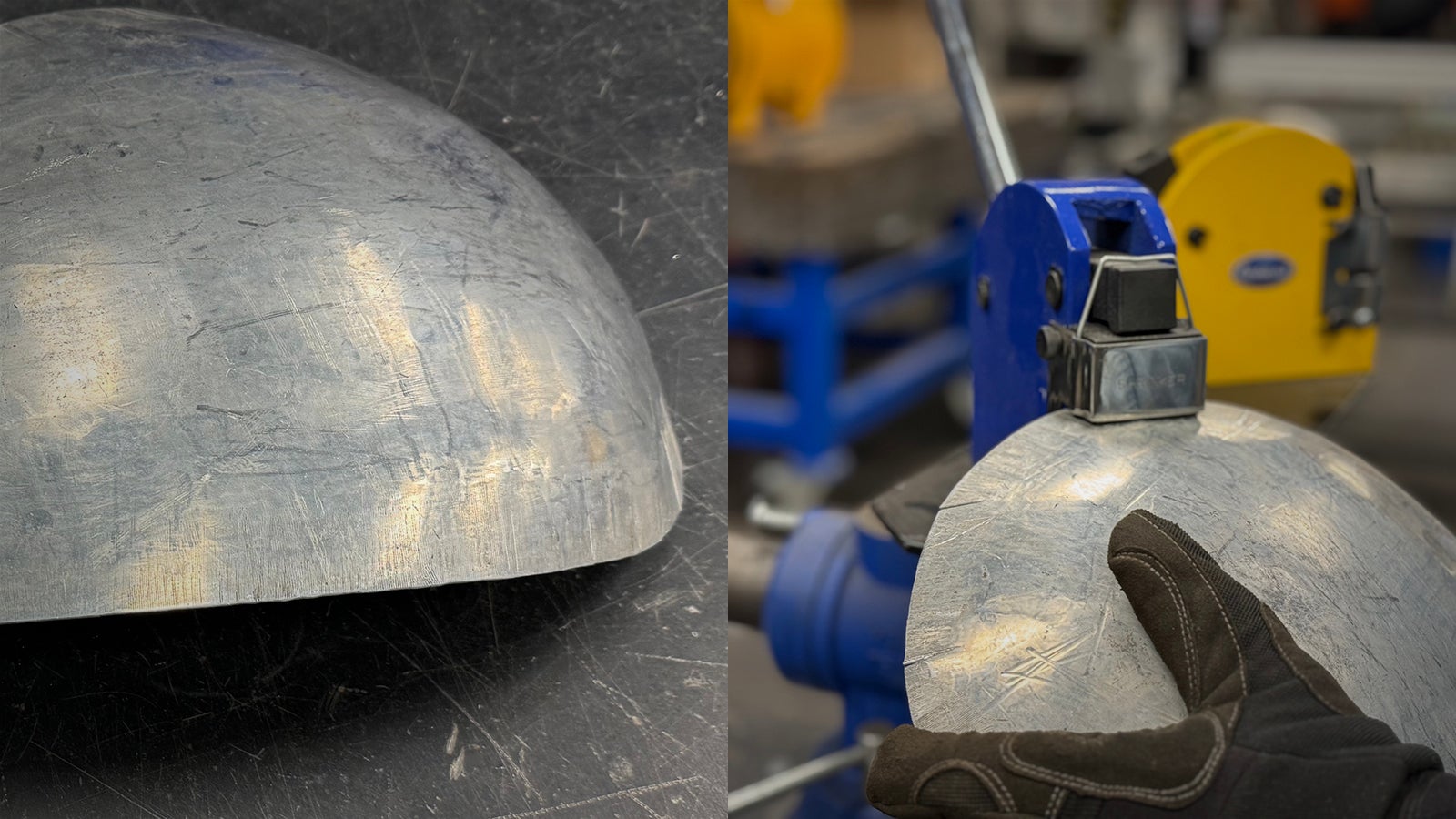
English Wheel
The English wheel is a metalworking tool used for forming smooth, compound curves in sheet metal. It consists of two large wheels – one fixed and one adjustable – that sandwich the metal as it is passed through, gradually shaping it into the desired contour.
English wheels are made in various sizes and designs, and they are crucial for creating complex and consistent curves in automotive panels, such as fenders or body panels. They also help smooth out hammered panels for more consistent surface finishes.
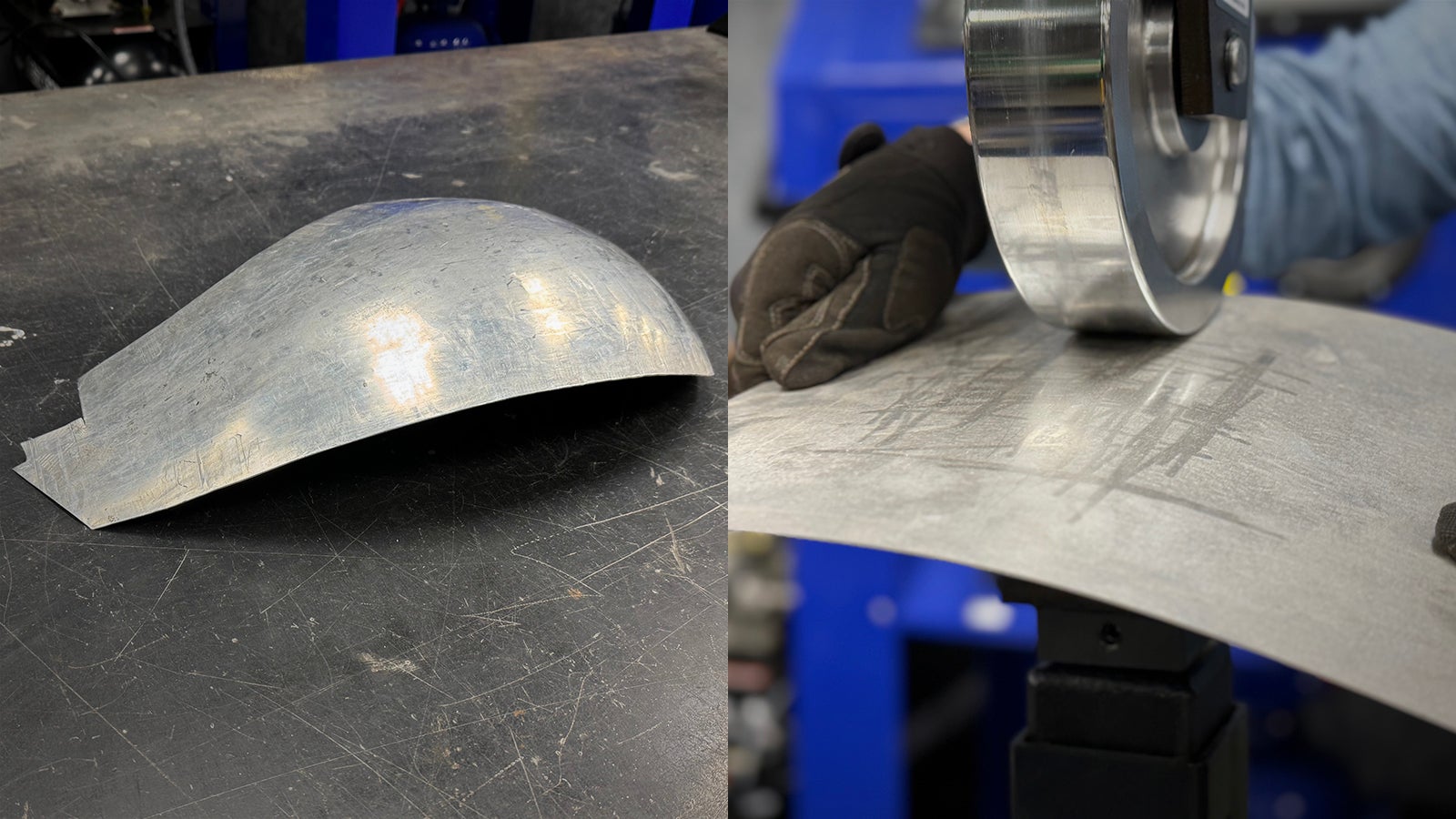
Flaring and Beading Punches
Flaring and beading involve creating flanges or raised edges on sheet metal to enhance a panel’s rigidity. Flaring is the process of creating a wider opening, while beading adds a rounded or decorative edge.
Specialized flanging and beading tools are utilized for these operations. This is often done with dies that shape and simultaneously punch holes in the metal, forming the desired profile. While often decorative, this process can reduce overall weight while adding strength to brackets, seatbacks, and other broad surfaces.
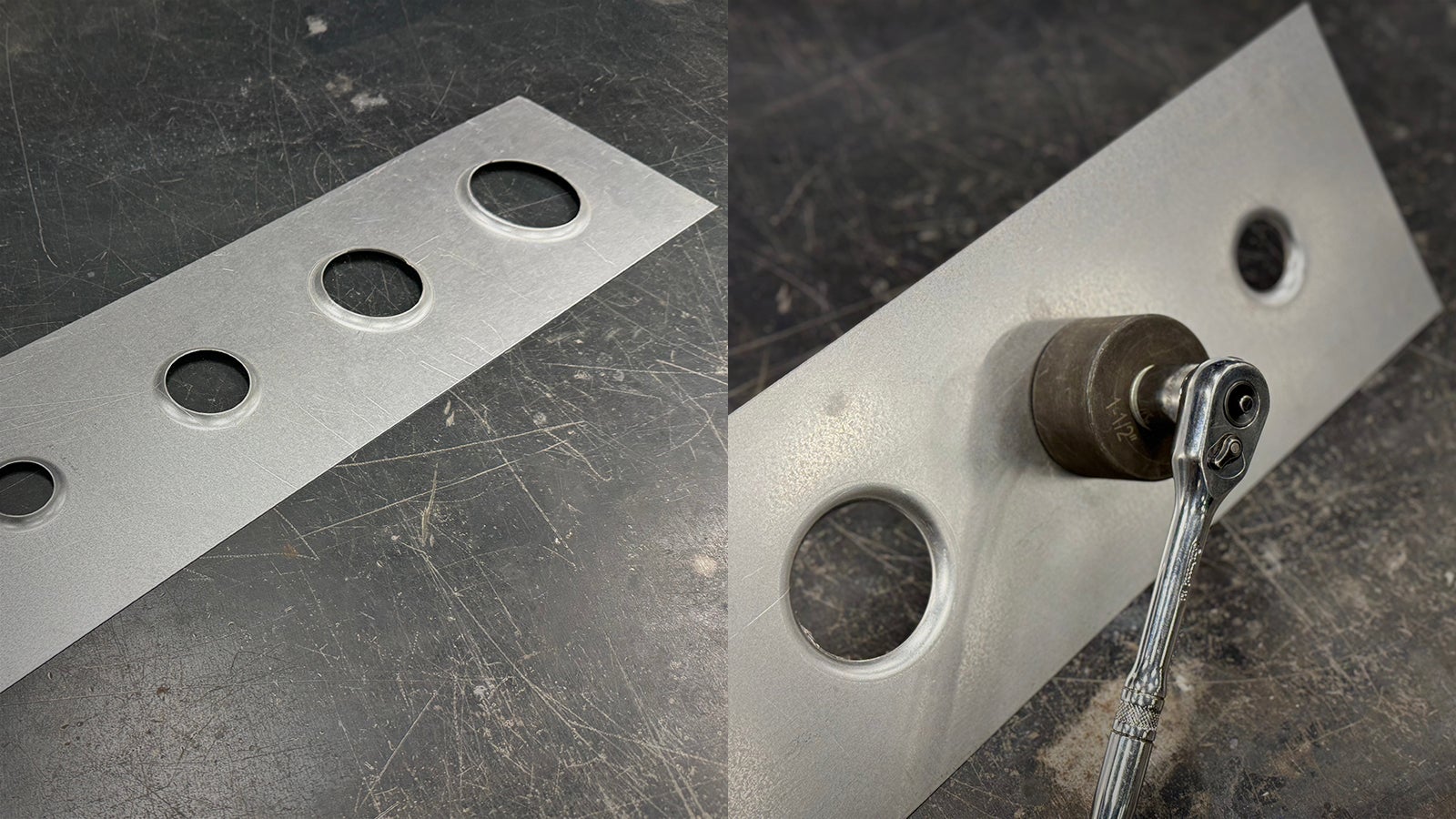
RESOURCES IN THIS ARTICLE
- Eastwood Versa Bend Sheet Metal Brake – Item # 14042
- Eastwood Panelbeater Sandbag and Teardrop Mallet – Item # 28045
- Eastwood Metal Bead Roller with Dies – Item # 32044
- Eastwood Shrinker/Stretcher Combo Set – Item # 51088
- Eastwood Benchtop English Wheel – Item # 14156
- Eastwood Metal Punch and Flaring Dies – Item # 20355